Excellence Through Engineering
Contact Info
(817) 556-2434
(888) 774-8802
[email protected]
Frankenstein Engine Dynamics, LLC.
2410 Ranger Hwy.
Weatherford, TX 76088
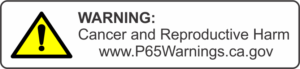
Excellence Through Engineering
Frankenstein determined an improved LS casting could deliver two things, more efficiency from reduced port turbulence and a Zen-like valve train that stays calm in extreme conditions. Everything had to change. And it did.
Development began in 2016 when Chris Frank, Brad Hall and Jesse Meagher agreed there was much more power potential for LS racing engines but existing castings had limitations. It was time for Frankenstein to design our own casting, with raised runners, 10° and 15° valve angle options and a valve train that scoffs at 10,000 rpm.
F-Series debuted at PRI in 2018. Engine builders knew it was special, a new raised runner cylinder head with features never seen before. But the industry didn’t buzz about it until later, when inexplicable dyno results started appearing. Then people wanted to know what we put into it.
Reactive Airflow Modeling – The Most Advanced Porting Method
The geometry of OEM LS castings have some limitations but the platform has exceptional power potential. But to make high performance a reality Frankenstein knew the castings had to change completely. That’s when the baby went out the window with the bathwater.
Starting with a clean slate has advantages, however, maintaining accessibility without compromising performance is a delicate balance. Frankenstein approached the F-Series design systemically with focus on each component. This strategy seeks to optimize the collective performance of the system to gain rewards measured in horsepower not flow numbers. In fact, CFM is never Frankenstein’s sole performance objective.
Cylinder head design has evolved since the flow bench came about 50 years ago. Flow bench CFM is still helpful, but it’s just a static measurement of air flow through a cylinder head. The reality is more bench airflow does not mean more horsepower. Today’s advanced porting methods incorporate the entire induction system to achieve maximum air speed, pressure recovery and combustion efficiency. Frankenstein designed the F-Series using Reactive Airflow Modeling, a proprietary approach to engineering peak performance in context of the whole induction system for its intended engine application. Optimal cylinder head designs emerge from advanced methods which incorporate the dynamics of air and fuel, turbulence, velocity, pressure, recovery and density occurring throughout the combustion process. We knew how to breathe life into the LS, but it needed a lot more than a new port program to reach maximum potential.
Frankenstein engineered the F-Series to run at such extreme levels that it pushed the boundaries of aftermarket components so we shared our prototypes and performance goals and visited partners like PAC and Jesel. They in turn stepped up and engineered new components compatible with the F-Series performance capabilities. Confident the F-Series could have a solid valve train, FED unleashed engineering to make our castings with the extreme airflow capabilities that we envisioned.
First order of business, was to exploit the raised runner design by raising the intake .250″ and raising the exhaust .200″. This substantial increase provides a more direct pathway for air but there was still room for improvement. So we repositioned the valve locations and moved the push rod which caused a hump along the intake wall. Repositioning the pushrod effectively reduced interference and opened the airpath further and served the dual purpose of improving alignment between the push rod and rockers. The F-Series exhaust ports were placed on center-line with the exhaust exit to improve spent hydrocarbon purging and the spark plug was centered in the chamber, for cleaner burn and maximum combustion efficiency. For practical purposes, the intake flange was extended to remain compatible with most OEM and aftermarket intakes.
Altogether, the flow characteristics exceeded expectations and are unmatched in the industry. The F-Series enables higher rpm ceiling while achieving peak torque earlier than currently available cylinder heads. The pressure, increased VE requires less timing to achieve peak power and optimal tuning.
Spintron tested to 10,000 rpm, the most stable valve train ever recorded by EFI.
Forces acting on the valve train cause components to deflect and compress which will steal lift and duration, leaving horsepower on the table.
The valve train geometry was critical to support the capabilities of the F-Series. It was designed for high performance valve train components to transfer energy efficiently resulting in superior stability and durability. To this end, Frankenstein aligned the pushrods and rocker assembly in order to mitigate push rod deflection, lifters and rocker kits. Frankenstein developed triangulated and doweled 6061-T651 billet rocker stands. An industry first, which improves system rigidity under high-rpm/high-stress applications when using stock-style OEM or aftermarket rockers.
The F-Series is robust, accommodating up to 1/2″ push rods and it needs a rocker assembly to endure spring pressures of aggressive cam profiles. During the development phase, Jesel evaluated our prototypes and new steel billet rocker stands. The Jesel engineering team designed a custom shaft-mount rocker assembly with 1.80/1.80 ratio, and options to 2.0. The F-Series shaft rockers are a solid body 2024 aluminum construction which resists fatigue, stress and heat. The rockers are lighter weight and provide superior rigidity which is ideal for the high cylinder pressures of the F-Series. Jesel also mimicked the LS7 cup depth for close to stock preload and included a cup adjuster common with Jesel rockers.
Frankenstein also partnered with PAC to develop a custom 0.700 lift dual spring kit to endure higher rocker ratios, reduce loft, minimize oscillation in extreme conditions. Custom valves, guides and titanium retainers were also added for durability and increased longevity.
Cooling efficiency is engineered into the F-Series. -6 ORB water cross over ports provide optimal cooling capacity to ensure equalized temperatures between cylinders for precise and reliable tuning. The enhanced deck structure is comprised of a custom A356 aluminum for increased durability and to reduce the effects of heat sink. Finally, a high efficiency water jacket was added, designed using CAD and CFD modeling, to provide exceptional cooling capacity.
The outcomes: Frankenstein partnered with EFI University to Spintron test the F-Series. Analysis revealed the most stable LS valve train ever recorded by EFI U at 10,000 rpm.
High Efficiency Water Jacket. Designed using CAD and CFD modelling to provide exceptional cooling capacity without sacrificing strength.
Proprietary Valve Cover Flange Design. Extra wide flange pattern provides the clearance required for aftermarket shaft-mount rockers that traditional designs lack.
Dowelled Valve Cover Flange with O-Ring. Gasketless design increases serivceability and eliminates misalignment while providing a superior seal.
FED’s high performance billet rocker stands enhance the capabilities the F-Series when using OEM rockers. Designed for stability in high-rpm/high-stress applications, F-Series rocker stands are built to precise tolerances and maintain rigidity to minimize component flex and ensure maximum lift is achieved at peak power. FED’s billet rocker stands are triangulated and Dowelled 6061-T651 billet aluminum.
CHE Precision Bronze Valve Guides Standard.
6-Bolt Casting Standard. Compatible with all factory and aftermarket LSX engine blocks.
-6 ORB water crossover to increases cooling efficiency and equalizes cylinder head temperatures for more precise and reliable tuning. FED Coolant Crossover kits available.
Raised Runner Intake and Exhaust Ports. 0.250″ raised intake ports and 0.200″ raised exhaust ports significantly increase cylinder head efficiency and flow characteristics in all high-HP and high-RPM applications. Intake flange is extended to remain compatible with most OEM and aftermarket intakes.
High temp silicone exhaust flange O-rings ensure consistent seal and ease of maintenance.
Moved LS7 Header Flange Bolt Pattern. 0.200″ moved pattern further increases exhaust port efficiency when combined with our raised runner design by aligning the port exit with the valve centerline.
CHE Precision Ductile Iron Seats Standard. Copper alloy seats are optional.
7/16″ Main Studs/8mm Under Studs Standard. 1/2″ main studs and 3/8″ under studs optional.
A357-T6 Aluminum Casting. This alloy is used in high end blocks and provides superior strength and longevity compared to lesser alloys including A356 and A319.
Enhanced Deck Structure to survive high HP and power adder applications. Dry deck configuration optional.